Zyvex Labs has created a unique Creep and Hysteresis model that has been very effective in dramatically reducing the position errors in piezoelectric actuators. We have done so as part of our research for DARPA, the Army Research Office, and the Advanced Manufacturing Office of the DOE.
Our application is for Scanning Tunneling Microscopes (STM) and this technology has been very effective in improving the accuracy of STM Lithography and STM images. Our proprietary model predicts the effects of creep and hysteresis and can modify the signal (in the digital regime) to the piezo actuator to achieve the desired motion
The DOE has asked us to determine if this technology would be useful to other users of piezoelectric actuators, which is why we are reaching out to your company. We are hoping you can help us understand if this is useful technology.
First, we would like to share some data demonstrating the success of our Creep and Hysteresis Correction (CHC) technology with respect to STM operation which uses open-loop piezo tubes to scan the tip. In the example below we jump 500nm to the right and then scan back and forth over the same line for 200S.
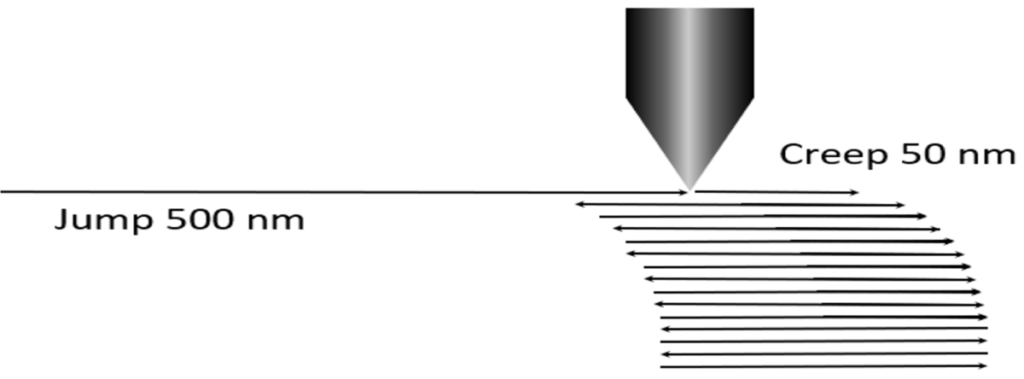
After a 500nm jump and scanning only in X for 200s, the curvature on the left is an uncorrected creep. On the right, the vertical lines indicate corrected creep.
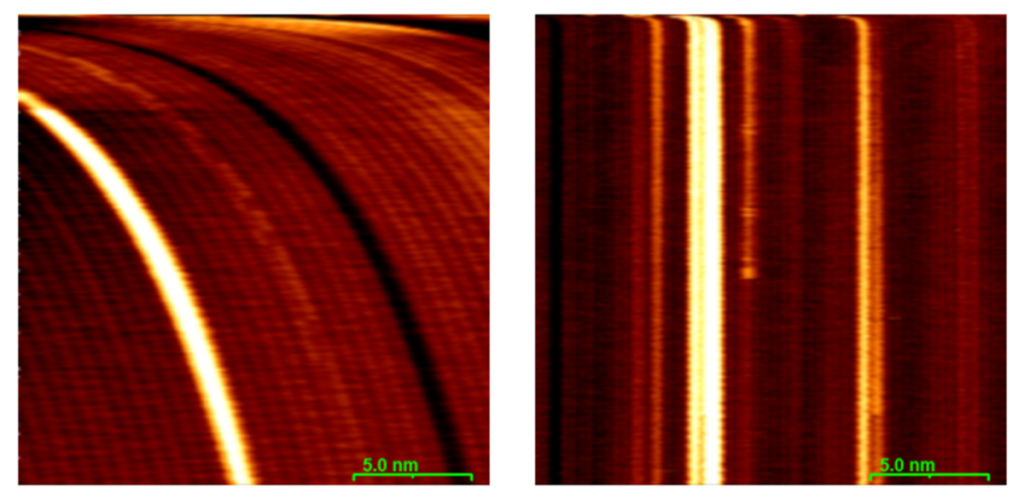
In this example we move the STM tip down toward the surface by 200nm and once in tunneling range, the current control loop is turned on which adjusts the tip height to keep a constant setpoint current. With the current loop on, the tip height above the surface is maintained at about 1nm. However, with CHC not engaged, because of creep the control loop must raise the tip by about 20nm as the creep moves the tip toward the surface.
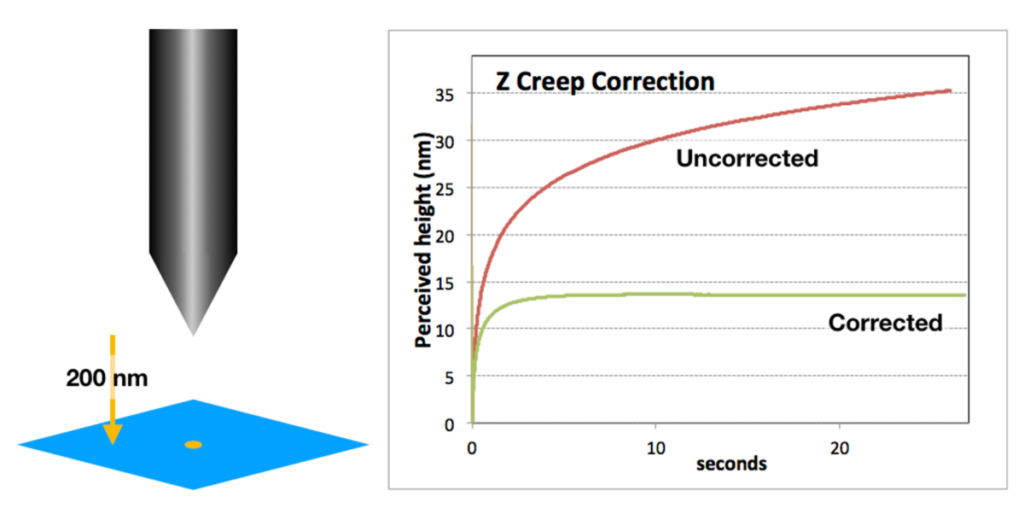
This data compares the experimental position (measured with an interferometer) data of a single axis piezo actuator with the ideal linear response. The time-varying creep error is linear with the size of the deflection and its order of magnitude is about 10%. The hysteresis error is not time-varying, but its order of magnitude error varies quadratically with displacement. The creep and hysteresis produce an RMS error of 1013nm. This data shows the same experimental displacement, our model’s prediction of the displacement, and the model’s error in predicting the experimental data. The RMS error is reduced from 1013nm to 77nm.
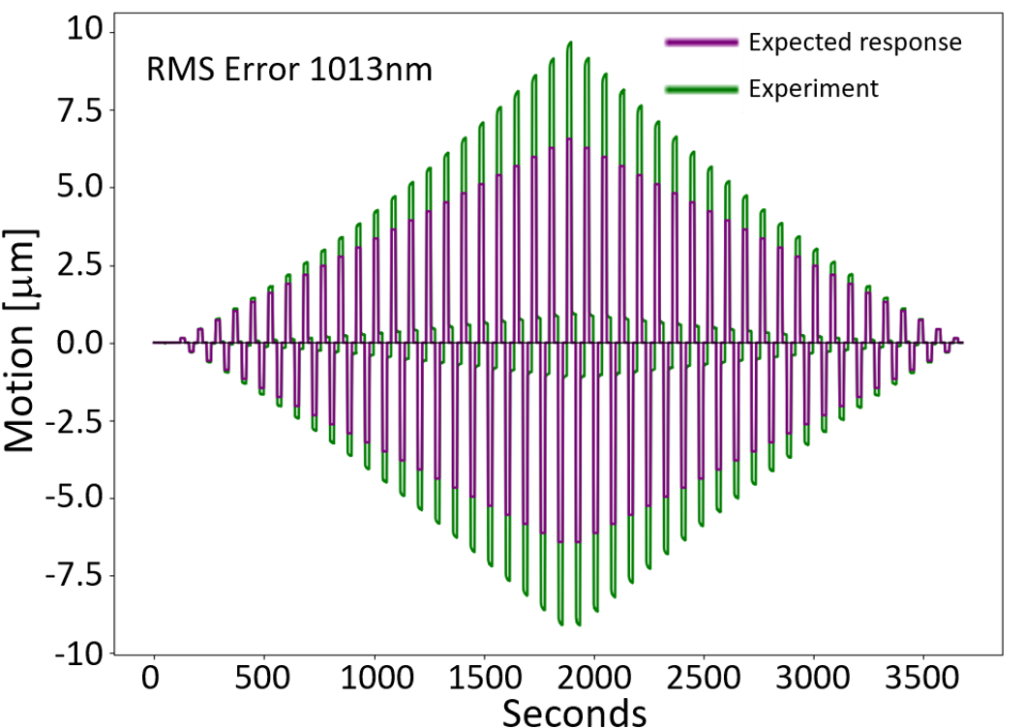
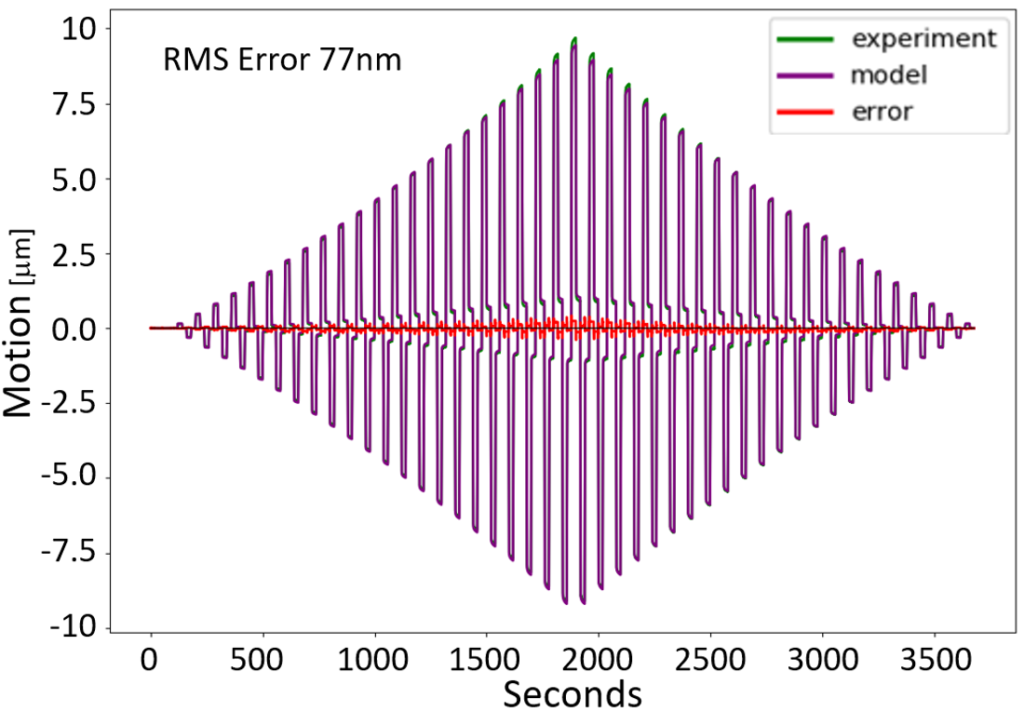
Some Details
- Calibration is required, but we have routines on the STMs that make calibration of our model straightforward.
- Depending on the application, either calibration of the piezo element can be done at the factory, or some calibration capability can be included in the product or as a separate product.
- For the STM allocation we need to calculate and correct the creep and hysteresis every 10 microseconds which requires significant low latency computational power requiring relatively expensive hardware.
- For control systems with much lower bandwidth requirements very modest and inexpensive computational power are adequate.
- For open loop systems with no or not very effective correction methods, we think that this technology could be very useful.
- To our surprise we have found at least one customer with a closed-loop application where our CHC model linearizes the actuator response and seems to improve the control systems accuracy.
We would like your opinion:
- Do you think that this technology could be useful for correcting creep and hysteresis in nanopositioning systems?
- If so, what nanopositioningapplications would you recommend that we consider?
- Is measuring the RMS error of the corrected experimental motion versus an ideal linear response over a large range of positive and negative motions and 20 second delays between moves a good metric?
- Are there better metrics to use to judge the effectiveness of the correction technique?
- What other advice about the value of this technology could you share?
Regards, John Randall – jrandall@zyvexlabs.com